Process analyzers measure the concentration of specific substances for the purpose of measuring and/or controlling those concentrations in a process stream. Safety analyzers detect the presence of dangerous concentrations of specific substances to warn personnel of threats to life or health. While there is virtually no end to the different types of process analyzers in existence, with new analyzer types invented to meet the needs of process industries, safety analyzers are rather restricted to those substances known to pose health hazards to human beings.
Safety analyzers are designed for fast response, rugged construction, and ease of portability. As such, they are usually not as accurate or as sensitive to slight changes in concentration as process analyzers. The sensing technologies used in safety analyzers are often very different from those used in process analyzers. You will never, for example, see an NDIR instrument with a Luft-style “microphone” detector used for portable safety applications66 . The high accuracy of a Luft-style NDIR instrument is not necessary for safety, and the bulk (and fragility) of such an instrument makes it completely impractical as a portable device.
An important industrial application of safety gas analyzer technology is testing the safety of the atmosphere inside a confined space, such as an industrial vessel that has been emptied in preparation for workers to enter and perform maintenance work. Virtually all pressure vessels are classified as confined spaces from the perspective of internal maintenance work, and many are explicitly labeled as such to remind workers of the danger:
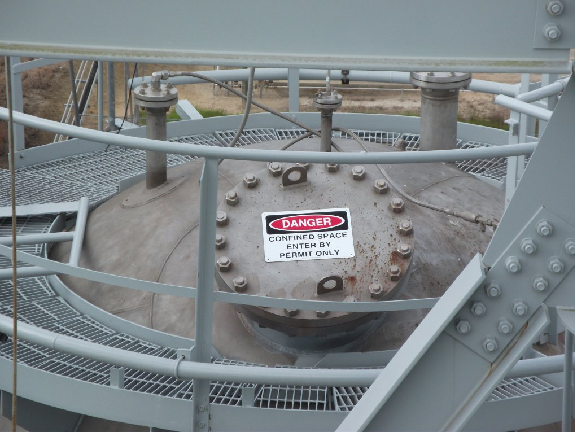
This photograph shows a hand-held safety gas monitor, used to detect four different gases with known hazard levels (oxygen, carbon monoxide, combustibles, and hydrogen sulfide). A technician working in hazardous environments would wear one of these at all times, listening for the audible warning tone generated by the device if any of its pre-set limits is exceeded:
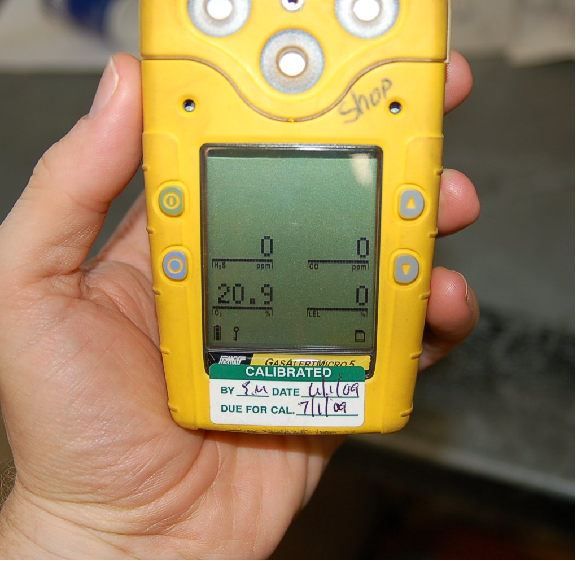
Most portable gas analyzers such as this employ electrochemical sensing “cells” generating a small electric current when exposed to the gas of interest. Such technologies may not always be the most accurate or the most sensitive, but their characteristics are well suited for portable applications where they will be exposed to vibration and must operate on battery power.
A close-up photograph taken of the monitor’s alarm thresholds reveals the relative concentrations of four gases monitored by the device. Two distinct alarm levels – “low” (alert) and “high” (danger) – exist to warn the user of threats:
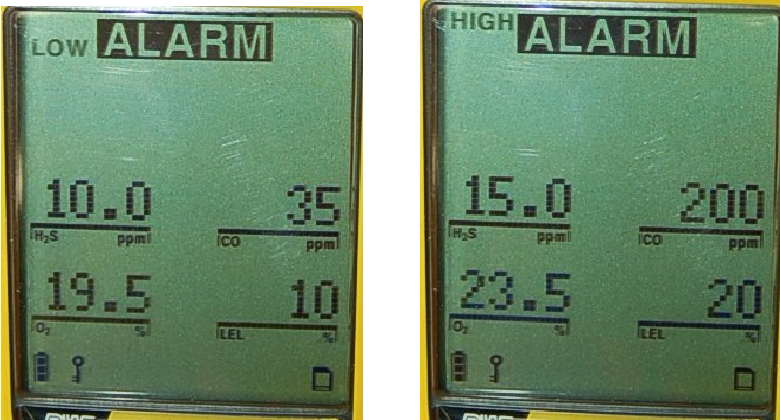
The two most dangerous gases detected by this device – hydrogen sulfide (H2S) and carbon monoxide (CO) – are measured in units of parts per million, or ppm. The next two detected gases – oxygen (O2) and combustibles (“LEL”) – are measured in units of percent (which may be thought of as parts per hundred).
Like all safety-related devices, portable gas analyzer require regular “proof-testing” and calibration. In order to accurately check the response of a gas analyzer, it must be exposed to gases of known concentrations. Special mixtures of “test gas” for safety analyzers are available from chemical supply companies, the next photograph showing the certified concentrations of different gases contained inside the pressurized test cylinder:
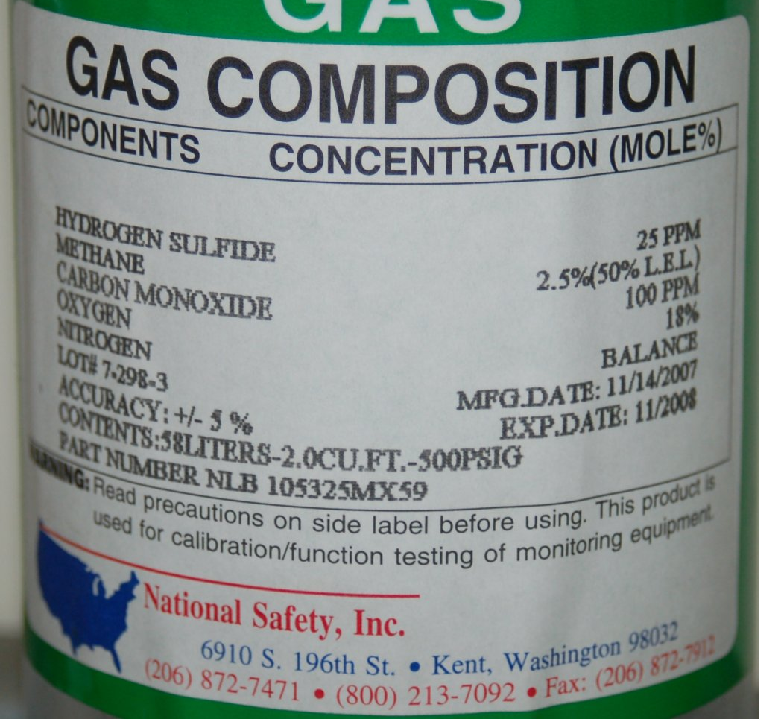
Note the limited shelf life of this span gas: only one year between its date of manufacture (November 2007) and its expiration (November 2008). Relatively short expiration periods are common with chemical standards used for analytical calibration, owing to slow chemical reactions between the constituent compounds over time altering the composition of the mixture. In this test gas cylinder, for example, the relatively high concentration of oxygen gas (18%) will over time oxidize the hydrogen sulfide, methane, and carbon monoxide gases, resulting in decreased concentrations of all these gases, with the production of water vapor and other oxides (e.g. CO2) inside the gas cylinder.
23.12.1 Oxygen gas
Most living things require oxygen to survive. The oxygen you breathe combines with nutrients from the food you eat to produce energy in a form usable by your body. If you are deprived of oxygen, your body very quickly shuts down, much like a fire dies when starved of oxygen (and for approximately the same reason). Ambient air is approximately 20.9% oxygen by volume, the majority of air (about 78% by volume) being nitrogen.
The oxygen content of air may be reduced by combustion (which combines oxygen with flammable substances to produce carbon dioxide and water vapor) or by displacement by a denser gas (such as propane) in a low-lying area or by any gas in sufficient quantity filling an enclosed area.
A modern oxygen sensor technology for safety applications is the micro fuel cell, generating a measurable electric current in the presence of oxygen by the oxidation of a self-contained fuel source. In many sensors, the fuel is pure lead (Pb), with the resulting chemical reaction producing lead oxide (PbO):

Fuel cell sensors are relatively rugged, accurate, and self-powering, enabling their use in portable oxygen analyzers. Due to their principle of operation, where an internal fuel is slowly oxidized over time, these sensors have a rather limited life and therefore must be periodically replaced.
An interesting and useful technique for testing the operation of an oxygen safety sensor is to exhale on the sensor, watching for a decrease in oxygen content to 15% or below. This testing technique makes use of the fact that your body extracts oxygen from the air, such that your exhaled breath contains less oxygen than it did when inhaled. Therefore, your own body acts as a crude “calibration gas” source for an oxygen safety analyzer.
23.12.2 Lower explosive limit (LEL)
The minimum concentration of a flammable gas in air capable of igniting is called the Lower Explosive Limit, or LEL. This limit varies with the type of gas and with the oxygen concentration of the air in which the flammable gas is mixed. Sensors designed to detect the dangerous presence of combustible gases are therefore called “LEL sensors.”
LEL monitors are used whenever there is a high probability of explosive gases present in the air. These areas are referred to as classified areas in industry, and are precisely defined for safety engineering purposes. Classified areas harboring explosive gases or vapors are deemed Class I areas, with different “Group” categories delineating the specific gas or vapor types involved. For more information on classified areas, refer to section 32.1.1 beginning on page 4257.
Gases and vapors are not the only substances with the potential to explode in sufficient concentration. Certain dusts (such as grain) and fibers (such as cotton) may also present explosion hazards if present in sufficient quantity. Unfortunately, the majority of analytical technologies used to monitor lower explosive limits for safety purposes only function with gases and vapors (Class I), not dusts or fibers (Class II and Class III, respectively).
Popular sensor technologies used to detect the presence of combustibles in air include the following:
- Catalytic bead
- Thermocouple
- Infrared
- Flame ionization
Catalytic bead and thermocouple sensors both function on the principle of heat generated during combustion. Air potentially containing a concentration of flammable gases or vapors passes near a heated element, and any combustion occurring at that point will cause the local temperature to immediately rise. These sensors must be designed in such a way they will not initiate an explosion, but merely combust the sample in a safe and measurable manner. Like micro fuel cell oxygen sensors, these sensors may be manufactured in sufficiently small and rugged packages to enable their use as portable LEL sensors.
Infrared analyzers exploit the phenomenon of infrared (IR) light absorption by certain types of flammable gases and vapors. A beam of infrared light passed across a sample of air will diminish in intensity if significant concentrations of the combustible substance exist in that sample. Measuring this attenuation provides an indirect measurement of explosive potential. A major disadvantage of this technique is that many non-flammable gases and vapors also absorb IR light, including carbon dioxide and water vapor. In order to successfully reject these non-flammable substances, the analyzer must use very specific wavelengths of IR light, tuned to the specific substances of interest (and/or wavelengths tuned specifically to the substances of non-interest, as a compensating reference signal for the wavelengths captured by both the substances of interest and the substances of non-interest).
Flame ionization sensors work on the same principle as FIDs for chromatographs: a non-ionizing flame (usually fueled by hydrogen gas) will generate detectable ions only in the presence of air samples containing an ionizing fuel (such as a hydrocarbon gas). Of course, this form of LEL sensor is useless to detect hydrogen gas.
23.12.3 Hydrogen sulfide gas
Hydrogen Sulfide (H2S) is a highly toxic gas, with a pungent “rotten eggs” odor at low concentrations but no visible color. At higher concentrations, the gas acts as a nerve agent to de-sensitize human smell, so that it seems odorless. Its paralytic effect on smell extends to more important bodily functions such as breathing, causing rapid loss of consciousness and asphyxiation. A photograph of a safety chart (taken at a wastewater treatment facility) shows just how toxic hydrogen sulfide gas is:
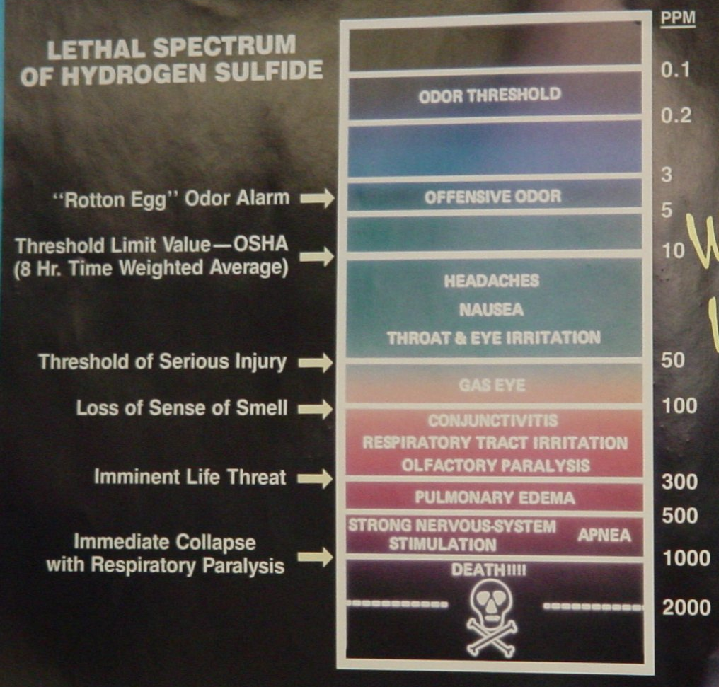
Note how concentrations in the parts per million range are hazardous, and how little H2S concentration is required to paralyze one’s sense of smell. Hydrogen sulfide also happens to be flammable, its LEL value in air being 4.3%. However, the toxic properties of the gas are generally the more pressing concern when released into the atmosphere. Another hazardous property of hydrogen sulfide is its density: 1.18 times that of air. This means H2S gas will tend to collect in low areas such as pits, electrical vaults, and empty underground storage vessels.
The principal source of hydrogen sulfide gas is anaerobic (oxygen-less) decomposition of organic matter. Sewage treatment facilities, pulp mills, and oil refineries generate H2S gas in significant quantity, and so employees at such facilities must be continually aware of the associated hazards.
One of the most popular analytical sensing technologies for H2S gas appropriate for portable monitoring includes an electro-chemical reaction cell similar in principle to the micro fuel cells used to detect oxygen concentrations. Hydrogen sulfide gas entering such a cell engages in a specific chemical reaction, creating a small electrical current proportional to the gas concentration. Like oxygen-sensing fuel cells, these chemical cells also have limited lives and must be routinely replaced.
23.12.4 Carbon monoxide gas
Carbon monoxide (CO) gas is a colorless, odorless, and toxic gas principally generated by the incomplete combustion of carbon-based fuels. The mechanism of its toxicity to people and animals is the preferential binding of CO gas molecules to the hemoglobin in blood. At significant concentrations of carbon monoxide gas in air, the hemoglobin in your blood latches on to CO molecules instead of oxygen (O2) molecules, and remains bound to the hemoglobin, preventing it from transporting oxygen. The result is that your blood rapidly loses its oxygen-carrying capacity, and your body asphyxiates from within. Like hydrogen sulfide, carbon monoxide is also flammable (LEL = 4%), but its toxic properties are generally the larger concern when released into the atmosphere.
Carbon monoxide is not to be confused with carbon dioxide (CO2) gas, which is almost completely inert to the human body. Carbon dioxide is principally produced by complete combustion of carbon-based fuels. Its only safety hazard potential is the capacity to displace breathable air in an enclosed area if rapidly released in large volumes.
Combustion burners operating on carbon-based fuels may produce excess carbon monoxide if operating at too rich an air/fuel mixture. Even when adjusted optimally, there will always be some carbon monoxide present in the exhaust. This makes high CO concentrations possible where burners operate in enclosed areas.
Some industrial processes such as catalytic cracking in the petroleum refining industry generate huge amounts of carbon monoxide, but these extremely high concentrations are normally present only within the process piping and vessels, not released to atmosphere. Nevertheless, personnel working near such processes must wear portable CO gas safety monitors at all times to warn of leaks.
Carbon monoxide may be sensed by an electrochemical cell, using iodine pentoxide as the reacting compound. The balanced chemical reaction is as follows:

The strength of the electric current produced by the cell indicates the concentration of carbon monoxide gas.
23.12.5 Chlorine gas
Chlorine (Cl2) gas is a strong-odored, toxic gas used as a biological disinfectant, bleaching agent, and as an oxidizer in many industrial processes. Colorless in low concentrations, it may appear green in color when mixed in very high concentrations with air. Chlorine is highly reactive, presenting a distinct hazard to mucus membranes (eyes, nose, throat, lungs) by creating hypochlorous acid (HOCl) and hydrochloric acid (HCl) upon contact with water:

The following table correlates levels of chlorine gas concentration in ambient air with degree of hazard. Note the unit of measurement for chlorine concentration in air – parts per million (ppm). Bear in mind that one part per million is equivalent to just 0.0001 percent:
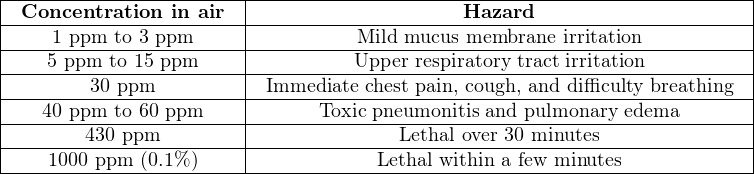
Water and wastewater treatment operations frequently67 use chlorine for disinfection of water. Pulp mills use either chlorine or chlorine compounds as a bleaching agent to whiten wood pulp.
Chlorine may be generated on site by the electrolytic decomposition of salt (sodium chloride – NaCl), or delivered in cylindrical pressure vessels in liquid form as shown here at a large wastewater treatment facility:
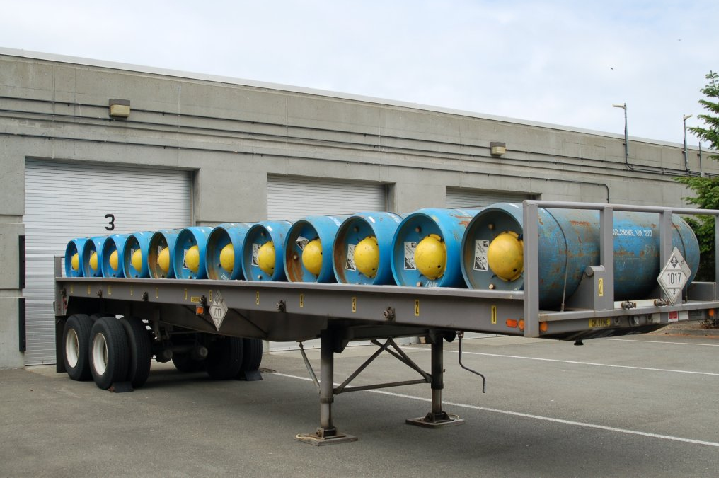
23.13 Review of fundamental principles
Shown here is a partial listing of principles applied in the subject matter of this chapter, given for the purpose of expanding the reader’s view of this chapter’s concepts and of their general inter-relationships with concepts elsewhere in the book. Your abilities as a problem-solver and as a life-long learner will be greatly enhanced by mastering the applications of these principles to a wide variety of topics, the more varied the better.
- Conservation of energy: energy cannot be created or destroyed, only converted between different forms. Relevant to optical analyses, particularly fluorescence where the energy of a photon emitted by fluorescence is always less (never more) than the incident photon, the difference between the two photons’ energies being dissipated in the form of heat.
- Conservation of mass: mass is an intrinsic property of matter, and as such cannot be created or destroyed. Relevant to chemical reactions, where the total mass of the reaction’s products must precisely equal the total mass of the reactants.
- Kirchhoff’s Voltage Law: the algebraic sum of all voltages in a loop is equal to zero. Relevant to conductivity and pH sensor circuits, as well as bridge circuits used in a variety of analytical instruments.
- Ideal Gas Law: PV = nRT, describing the relationship between gas pressure, chamber volume, gas quantity (in moles), and gas temperature. Relevant to expansion of gas inside Luft detectors (NDIR instruments).
- Common logarithms: used to express measurements spanning a tremendous range. Relevant to pH calculations, where the pH of an aqueous fluid is the negative logarithm of its hydrogen ion activity (molarity) pH = −log[H+]. Also used to calculate absorbance of light by different substances (the Beer-Lambert Law A = log I0 I ).
- Self-balancing opamp circuits: all self-balancing operational amplifier circuits work on the principle of negative feedback maintaining a nearly zero differential input voltage to the opamp. Making the “simplifying assumption” that the opamp’s differential input voltage is exactly zero assists in circuit analysis, as does the assumption that the input terminals draw negligible current.
- Nernst equation: V = RT nF ln predicting the amount of voltage developed across an ion-permeable membrane by the exchange of ions across that membrane. Relevant to all forms of potentiometric chemical analysis, where sensor voltage is proportional to the logarithm of concentration quotient across the sensor membrane.
- Time constant: (τ), defined as the amount of time it takes a system to change 63.2% of the way from where it began to where it will eventually stabilize. The system will be within 1% of its final value after 5 time constants’ worth of time has passed (5τ). Relevant to pH measurement where signal voltage changes are damped by cable capacitance (forming an RC time constant).
- Integration (calculus): where one variable is proportional to the accumulation of the product of two others. Integration always results in a multiplication of units. Relevant to calculations of mass passing through a chromatograph detector: total mass of a species passed through the detector (m) equal to the integral of mass flow rate times time: m = ∫ W dt.
- Quantization of photon energy: E = hf, where the energy carried by each photon (particle of light) is a fixed quantity proportional to the frequency (color) of that photon. Relevant to spectroscopy, where different colors of light interact with substances depending on the energy levels associated with electrons around the atoms of the substance.
References
“Automated Measuring System Technologies”, Best Practice brochure, Cleaner Fossil Fuels Programme, document BPB008, DTI, 2004.
Annino, Raymond; Villalobos, Richard, Process Gas Chromatography – Fundamentals and Applications, Instrument Society of America, Research Triangle Park, NC, 1992.
Boylestad, Robert L., Introductory Circuit Analysis, 9th Edition, Prentice Hall, Upper Saddle River, NJ, 2000.
Carroll, Grady C., Industrial Process Measuring Instruments, McGraw-Hill Book Company, Inc., New York, NY, 1962.
Chu, P.M.; Guenther, F.R.; Rhoderick, G.C.; Lafferty, W.J.; “The NIST Quantitative Infrared Database”, Journal of Research of the National Institute of Standards and Technology, Volume 104, Number 1, Gaithersburg, MD, January-February 1999.
Fribance, Austin E., Industrial Instrumentation Fundamentals, McGraw-Hill Book Company, New York, NY, 1962.
Gregory, C.H.; Appleton, H.B.; Lowes, A.P.; Whalen, F.C.; Instrumentation and Control in the German Chemical Industry, Mapleton House, Brooklyn, NY, 1947.
“Investigation Report – Chlorine Release”, Report number 2002-04-I-MO, U.S. Chemical Safety and Hazard Investigation Board, Washington DC, 2003.
Jernigan, J. Ron, Chemiluminescence NOx and GFC NDIR CO Analyzers For Low Level Source Monitoring, Thermo Environmental Instruments, Franklin, MA.
Kanai, Hideo; Nakamura, Yusuke; Koizumi, Kazuhiro; “ZSS Cross Stack Laser Gas Analyzer”, Fuji Electric Review, Volume 54, Number 3.
Kohlmann, Frederick J., What Is pH, And How Is It Measured?, Hach Company, 2003.
Kuiken, Tim; Crabbe, Keith; “Tunable Diode Laser Spectroscopy Detection Principles For Monitoring NH3, HCl & HF”, CEMTEK Environmental, Inc., 2011.
Kume, Hidehiro, Photomultiplier Tube – Principle to Application, Hamamatsu Photonics K.K., 1994.
Lavigne, John R., Instrumentation Applications for the Pulp and Paper Industry, Miller Freeman Publications, Foxboro, MA, 1979.
Lipták, Béla G. et al., Instrument Engineers’ Handbook – Process Measurement and Analysis Volume I, Fourth Edition, CRC Press, New York, NY, 2003.
Luft, Von K.F., “Über eine neue Methode der registrierenden Gasanalyse mit Hilfe der Absorption ultraroter Strahlen ohne spektrale Zerlegung”, Zeitschrift für technische Physik, Vierundzwanzigster Jahrgang, Number 5, pp. 97-105, 1943.
“Multiple Component Real Time Impurity & Process Composition Analysis Using Mid IR Process Analytical Tunable Laser Spectroscopy (PATLS)”, document QCL-TWP-Mid-IR-PATLS, Emerson Process Management, October, 2015.
Novak, Joe, What Is Conductivity, And How Is It Measured?, Hach Company, 2003.
Pauling, Linus, General Chemistry, Dover Publications, Inc., Mineola, NY, 1988.
“pH Electrode Cleaning and Maintenance Guide”, document LIT2781 D12, Hach Company, 2012.
Scott, Raymond P.W., Gas Chromatography, Library4Science, LLC, 2003.
Scott, Raymond P.W., Gas Chromatography Detectors, Library4Science, LLC, 2003.
Scott, Raymond P.W., Liquid Chromatography, Library4Science, LLC, 2003.
Scott, Raymond P.W., Liquid Chromatography Detectors, Library4Science, LLC, 2003.
Scott, Raymond P.W., Principles and Practice of Chromatography, Library4Science, LLC, 2003.
Sherman, R.E.; Rhodes, L.J., Analytical Instrumentation: practical guides for measurement and control, ISA, Research Triangle Park, NC, 1996.
Shinskey, Francis G., pH and pION Control in Process and Waste Streams, John Wiley & Sons, New York, NY, 1973.
Skoog, Douglas A.; Holler, F. James; Nieman, Timothy A., Principles of Instrumental Analysis, Saunders College Publishing, Harcourt Brace College Publishers, Philadelphia, PA, 1998.
Soleyn, Ken, “Development of a Tunable Diode Laser Absorption Spectroscopy Moisture Analyzer for Natural Gas”, GE Sensing and Inspection Technologies, Rotterdam, 2009.
“Standard Operating Procedures – Thermo Environmental Instruments Model 43C Trace Level Pulsed Fluorescence Sulfur Dioxide Analyzer”, version 2.0, Environmental Protection Agency, Research Triangle Park, NC, 2009.
Theory and Practice of pH Measurement, PN 44-6033, Rosemount Analytical, 1999.
“XSTREAM Gas Analyzer Series Instruction Manual”, document HASX2E-IM-HS, Rosemount Analytical, 2009.