A proximity switch is one detecting the proximity (closeness) of some object. By definition, these switches are non-contact sensors, using magnetic, electric, or optical means to sense the proximity of objects.
Recall from section 9.1 that the “normal” status of a switch is the resting condition of no stimulation. A proximity switch will be in its “normal” status when it is distant from any detectable object.
Being non-contact in nature, proximity switches are often used instead of direct-contact limit switches for the same purpose of detecting the position of a machine part, with the advantage of never wearing out over time due to repeated physical contact.
Most proximity switches are active in design. That is, they incorporate a powered electronic circuit to sense the proximity of an object. Inductive proximity switches sense the presence of metallic objects through the use of a high-frequency magnetic field. Capacitive proximity switches sense the presence of non-metallic objects through the use of a high-frequency electric field. Optical proximity switches detect the interruption of a light beam by an object. Ultrasonic proximity switches sense the presence of dense matter by the reflection of sound waves.
The schematic diagram symbol for a proximity switch with mechanical contacts is the same as for a mechanical limit switch, except the switch symbol is enclosed by a diamond shape, indicating a powered (active) device:
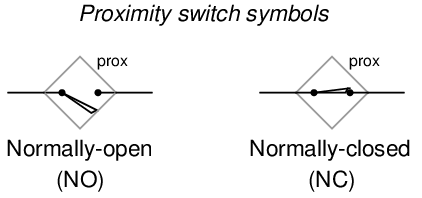
Many proximity switches, though, do not provide “dry contact3 ” outputs. Instead, their output elements are transistors configured either to source current or sink current. The terms “sourcing” and “sinking” are best understood by visualizing electric current in the direction of conventional flow rather than electron flow.
The following schematic diagrams contrast the two modes of switch operation, using red arrows to show the direction of current (conventional flow notation). In both examples, the load being driven by each proximity switch is a light-emitting diode (LED):
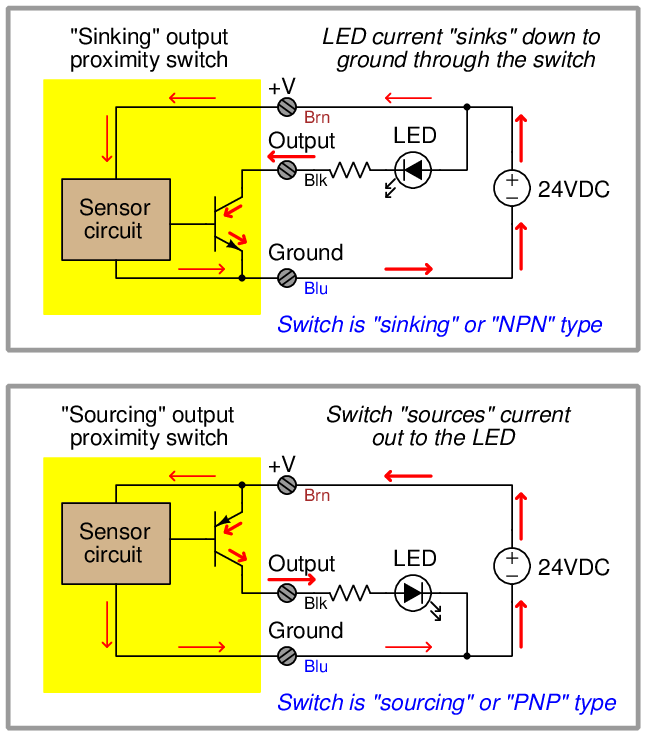
A common coloring convention for electronic proximity switches is brown for +V power supply, blue for ground (− pole of power supply), and black for the switched output signal. This convention is common to sinking and sourcing proximity switches alike.
An electronic switch designed to sink current through its signal wire is alternatively referred to as an NPN switch due to the type of transistor used in its output. Conversely, an electronic switch designed to source current through its signal wire may be referred to as a PNP switch. The key to understanding these labels is to recognize the emitter terminal of the output transistor is always the one connected to the power supply rail. For a sinking switch, this means the emitter must connect to the negative rail, necessitating4 an NPN transistor to do the switching. For a sourcing switch, this means the emitter must connect to the positive rail, in which case only a PNP transistor will suffice.
Yet another convention for describing sourcing and sinking transistor switches is to refer to them as high-side switches and low-side switches, respectively. A sourcing transistor (PNP) has its emitter terminal attached directly to the “high” rail (+) of the DC power supply. A sinking transistor (NPN), by contrast, has its emitter terminal attached directly to the “low” rail (−) of the DC power supply.
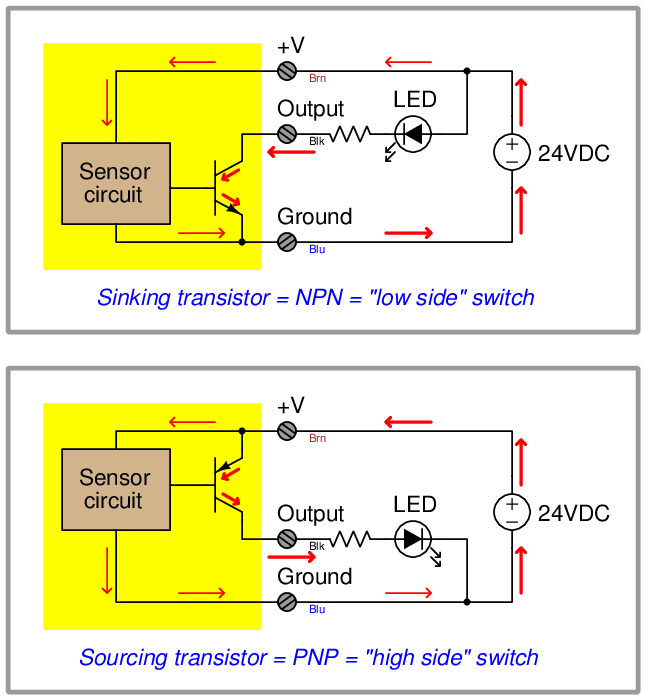
These photographs show two different styles of electronic proximity switch:
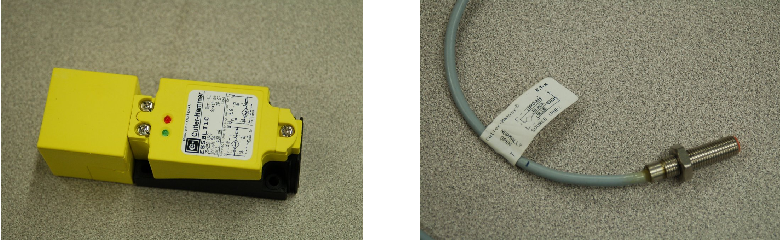
Many industrial proximity switches have built-in LED indicator lamps to help technicians diagnose circuit problems by directly indicating switch status. With just a glance, one may tell whether or not the proximity switch is detecting the presence of an object.
The next photograph shows a proximity switch detecting the passing of teeth on a chain sprocket, generating a slow square-wave electrical signal as the sprocket rotates. Such a switch may be used as a rotational speed sensor (sprocket speed proportional to signal frequency) or as a broken chain sensor (when sensing the rotation of the driven sprocket instead of the drive sprocket):
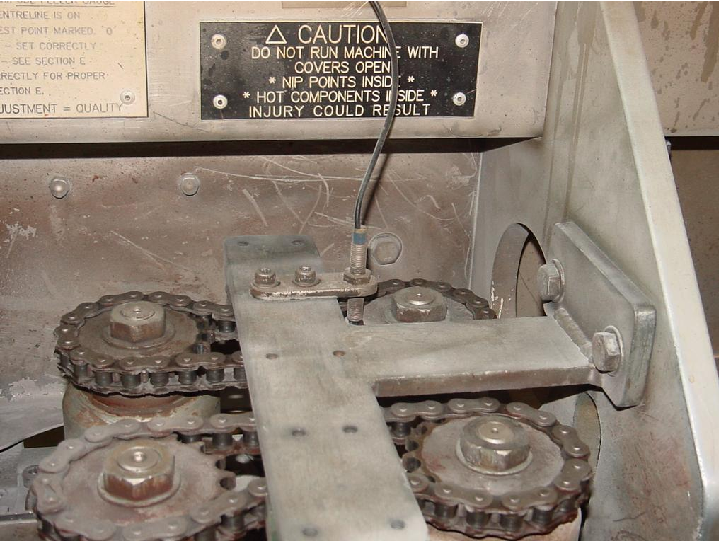
Like other types of process switches, proximity switches come in both “normally open” (NO) and “normally closed” (NC) varieties. This distinction has nothing whatsoever to do with sourcing versus sinking (PNP vs. NPN), but rather what the status of the proximity switch will be when no objects are near. Thus, it is possible to find normally-open proximity switches that are sinking (NPN) as well as normally-open proximity switches that are sourcing (PNP), and normally-closed proximity switches in either sinking or sourcing designs as well.
These switch characteristics are commonly fixed, and must be specified when ordering the device. Likewise, the detection range of a proximity switch is usually a fixed parameter rather than being adjustable.